Every 17 minutes, someone in New Zealand is seriously injured at work, with the construction industry ranking among the top five for workplace deaths and serious harm. Ensuring safety on construction sites isn’t just a legal obligation—it’s a critical responsibility to protect workers and prevent costly accidents. A well-executed safety audit can be the difference between a secure site and a potential disaster.
A construction site safety audit involves a detailed review of your site’s conditions, equipment, and practices to identify hazards and ensure compliance with health and safety regulations. By addressing risks proactively, you not only safeguard your team but also enhance your reputation as a responsible and reliable organisation. Whether you’re aiming to meet regulatory standards or exceed client expectations, understanding how to conduct an effective audit is essential for maintaining a safe and compliant workplace.
Understanding Construction Site Safety Audits
A construction site safety audit systematically reviews a site’s safety protocols, equipment, and working conditions. These audits aim to identify hazards and ensure adherence to New Zealand’s health and safety regulations.
What Is A Construction Site Safety Audit?
A construction site safety audit is a detailed evaluation of your site’s safety practices. It focuses on identifying potential risks, assessing compliance with current regulations, and improving overall onsite safety. The process involves examining incident records, equipment usage, and worker conditions. For instance, audits may assess how effectively personal protective equipment (PPE) is used or if scaffolding setups follow legal standards.
Two types of audits play key roles: program audits and system audits. Program audits evaluate the effectiveness of your existing safety procedures and address gaps in protocols, such as outdated policies or insufficient safety training. System audits evaluate your entire safety management framework, including policies that influence safety behaviour from management down to frontline staff. Both types ensure every aspect of the site promotes a secure working environment.
Importance Of Safety Audits In New Zealand
Safety audits remain crucial due to New Zealand’s high incidence of construction-related injuries and fatalities. Reports highlight that construction consistently ranks among the top industries for workplace harms. With someone injured every 17 minutes in the workplace nationwide, ensuring compliance with safety standards is vital.
These audits not only mitigate risks but also help your organisation align with New Zealand’s strict workplace safety regulations. By maintaining high standards, you benefit from reduced legal risks and avoid WorkSafe penalties. Also, many clients seek contractors with proven health and safety compliance, making robust safety audits a competitive advantage.
A well-executed safety audit ensures every detail, from equipment functionality to documentation, contributes to a safer, more accountable construction environment.
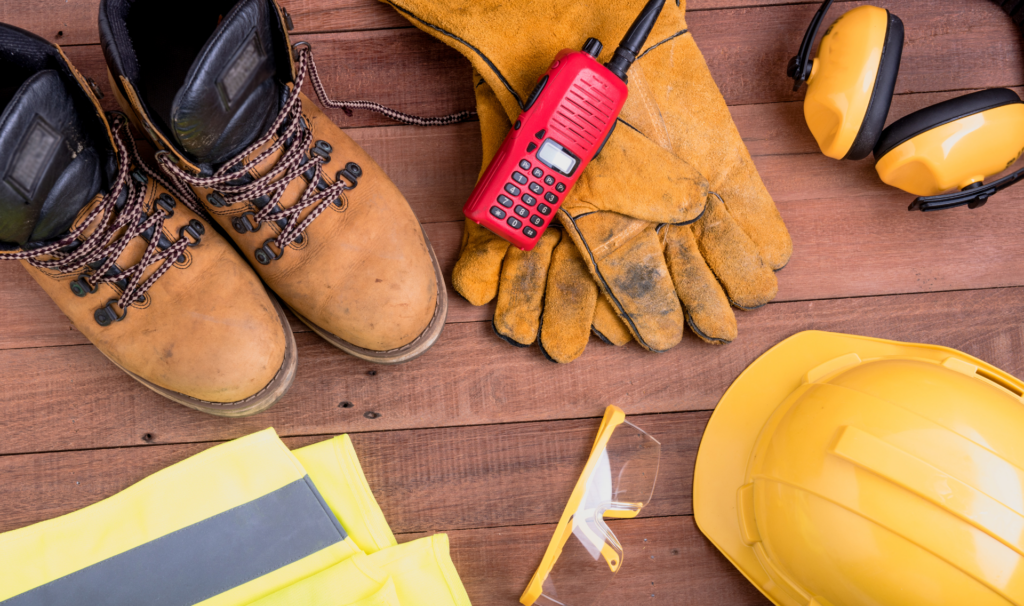
Preparing For A Safety Audit
Preparation is essential for a successful construction site safety audit in New Zealand. It ensures you cover every critical aspect required to assess compliance and identify potential hazards.
Identifying Key Safety Regulations In NZ
Familiarise yourself with New Zealand’s current Health and Safety laws. These include the Health and Safety at Work Act 2015 and associated regulations, which outline your responsibilities as a duty holder. Ensure any site-specific legislation related to hazardous substances, scaffolding, or construction is accounted for. Recognising these requirements sets a strong foundation for evaluating workplace compliance.
Gathering Necessary Documents And Records
Collect all legal documents, incident reports, safety procedures, and licensing records required for the audit. Include training records to verify employees’ certifications and risk management plans to assess emergency preparedness. Reviewing past audit results helps identify whether previous corrective actions have been implemented. Confirm all records are accurate and up to date to avoid incomplete documentation during the audit.
Assembling The Audit Team
Select a competent team to lead the audit. Include individuals with expertise in construction safety, site operations, and compliance standards. Internal staff and external consultants can provide valuable perspectives, ensuring objectivity during the process. Clearly define roles and responsibilities within the team to streamline inspection tasks and improve efficiency.
Conducting The Safety Audit
A construction site safety audit examines hazards, ensures compliance, and strengthens safety protocols. Follow structured steps to identify risks effectively.
Inspecting Site Conditions
Inspect the construction site thoroughly to evaluate potential risks. Check for structural integrity, fire hazards, emergency exit functionality, and overall site cleanliness. Look for poorly maintained scaffolding, uneven surfaces, or debris that could obstruct pathways. Verify that signage, such as hazard warnings and emergency procedures, is visible and clear. Note any areas requiring immediate remediation to prevent worker injuries.
Evaluating Equipment And Machinery
Inspect all equipment and machinery for operational safety. Confirm that all tools, machinery, and safety devices are well-maintained and free from wear or damage. Check safety guards, emergency shutoffs, and operator controls to ensure proper functionality. If equipment is not labelled with its maintenance history, address these documentation gaps. Confirm compliance with New Zealand’s equipment safety standards during this step.
Reviewing Worker Compliance And Training
Observe workers to assess compliance with safety regulations. Review their use of personal protective equipment (PPE), lifting techniques, and adherence to site safety rules. Interview employees about their understanding of safety procedures and knowledge of hazard mitigation. Cross-check this insight with training records, identifying gaps in safety education. Promote open discussions to address worker concerns and improve future training programmes.
Documenting Findings And Observations
Record all issues uncovered during the audit, categorising them by severity. Maintain organised documentation, including photographs, to support findings. Identify recurring patterns from past safety incidents alongside current gaps. Use these records as the foundation for an actionable improvement plan. This ensures your site aligns with New Zealand’s Health and Safety at Work Act 2015 requirements.
Post-Audit Steps
A detailed post-audit process ensures that the findings from your construction site safety audit lead to meaningful improvements. By systematically addressing identified issues, you can create a safer and more compliant work environment.
Analysing Audit Results
Review audit findings to determine the severity and impact of each identified risk. Focus on categorising hazards by their potential to cause harm, using criteria such as likelihood and severity. For example, prioritise high-risk hazards like unguarded machinery or unstable scaffolding. Ensure that all data, including inspection notes and incident patterns, is thoroughly evaluated to form a comprehensive risk profile for your site.
Developing Corrective Action Plans
Create action plans that address hazards based on their priority level. Include specific measures such as updating safety protocols, conducting targeted training sessions, or replacing non-compliant equipment. Assign each task to individuals or teams with clear deadlines for completion. For example, assign your maintenance team to inspect and repair faulty tools within two weeks. Ensure these plans align with New Zealand’s Health and Safety at Work Act 2015.
Monitoring Implementation of Changes
Regularly track the progress of corrective actions to confirm that all measures are effectively implemented. Conduct follow-ups like site inspections and review updated incident records to verify success. For example, check whether new protective barriers have been installed and if workers received their scheduled PPE training. Actively seek employee feedback on implemented changes to measure improvements in safety practices.
Tips For A Successful Safety Audit In NZ
- Plan ahead
Prepare for the audit by reviewing New Zealand’s Health and Safety at Work Act 2015. Compile relevant documents like safety procedures, incident reports, and training records to ensure a smooth and thorough process.
- Engage a qualified team
Use experienced safety auditors familiar with construction regulations and risks. Incorporate team members with specialised knowledge of the site’s operations to provide detailed insights.
- Inspect methodically
Examine key areas, including worksite conditions, equipment, and PPE use. Ensure safety signage is visible, machinery adheres to standards, and workers comply with safety protocols.
- Prioritise open communication
Encourage worker involvement by discussing the audit’s purpose and objectives. Use toolbox talks to address any hazards identified, fostering accountability and awareness.
- Document findings clearly
Record hazards and non-compliance issues with clear severity classifications. Use these findings to outline specific actions required to improve safety measures.
- Follow up consistently
Monitor the implementation of corrective actions through scheduled inspections. Confirm compliance with updated safety standards by consulting with workers and evaluating site conditions regularly.
Conclusion
Prioritising safety on construction sites in New Zealand is essential for protecting your workers and ensuring compliance with strict regulations. A well-executed safety audit not only identifies risks but also provides a roadmap for continuous improvement in workplace safety.
By committing to regular audits and following through with corrective actions, you create a safer environment while strengthening your organisation’s reputation and operational efficiency. Effective safety management is an investment in your team’s wellbeing and your company’s success.