Workplace safety is a critical concern for businesses, and understanding the regulations that govern it is essential for creating a secure environment. In New Zealand, WorkSafe NZ plays a pivotal role in promoting and enforcing health and safety standards, aiming to reduce workplace injuries, illnesses and fatalities. Their regulations cover everything from hazardous substances to machinery safety, ensuring comprehensive protection across industries.
Exploring these rules can seem daunting, but WorkSafe NZ provides tailored guidance to help you meet compliance requirements. From specific advice for sectors like agriculture and healthcare to training for health and safety representatives, these resources are designed to address the unique risks your business might face. By understanding these regulations, you’re not just meeting legal obligations—you’re fostering a safer, healthier workplace for everyone.
Understanding WorkSafe NZ Regulations
WorkSafe NZ regulations are designed to create safer workplaces and reduce risks. They apply to businesses of all sizes and cover a wide range of workplace safety aspects, including worker participation, hazardous substances, and emergency preparedness.
Worker Participation
Employees play a vital role in creating a safe workplace. WorkSafe regulations outline the formation of health and safety committees and appointing health and safety representatives. These representatives receive training to identify risks and ensure everyone’s voice is heard in safety decisions.
Hazardous Substances
Handling and storage of hazardous substances are strictly regulated to prevent accidents. The Hazardous Substances Regulations 2017 outline requirements for proper labelling, compliance certifications, and emergency management plans. For example, substances under pressure, like gases, must be stored in approved containers and tracked.
Emergency Preparedness
Every workplace must be ready to handle emergencies. Regulations include creating response plans, signage for hazards, and training workers to respond effectively. This ensures that workplaces are equipped to minimise harm during unexpected events.
Understanding and following these regulations helps you meet legal responsibilities while creating a safer environment for everyone.
Key Legislation And Framework
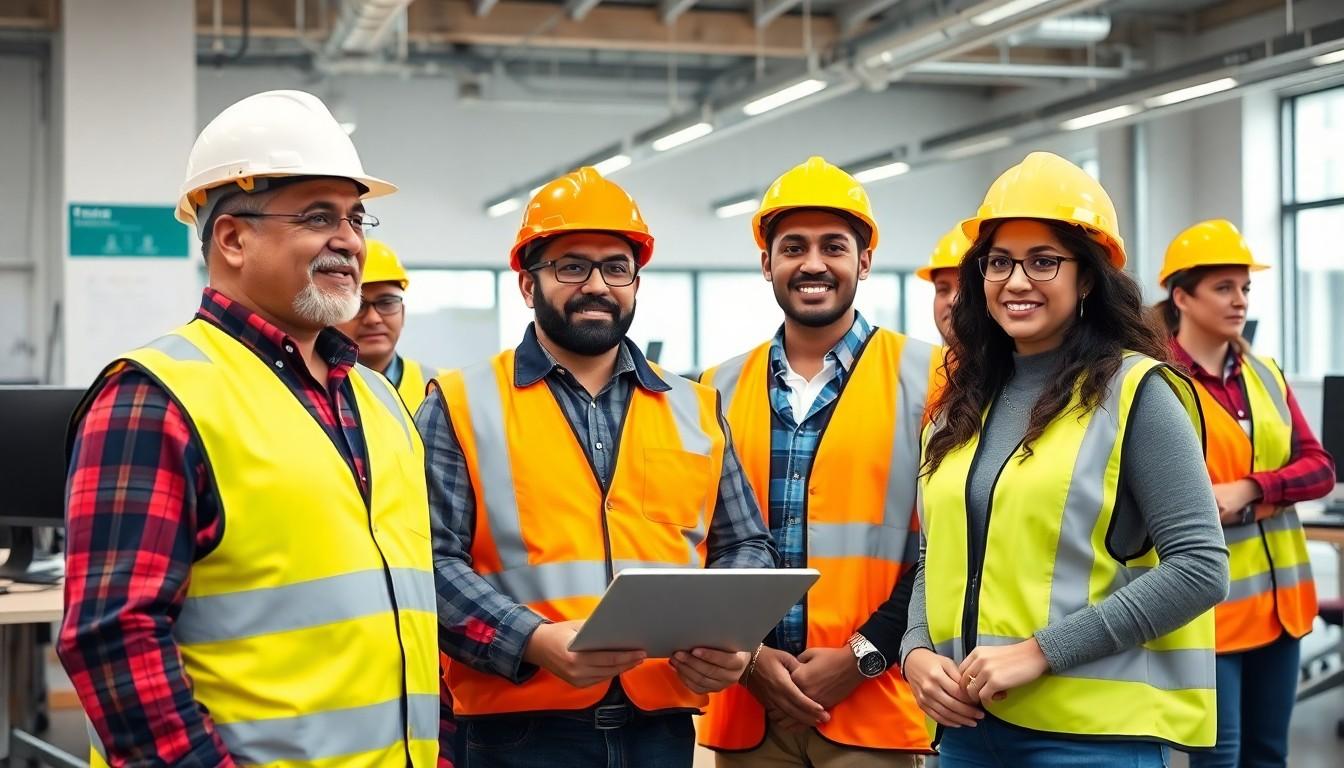
WorkSafe NZ regulations are primarily grounded in key laws and supporting guidelines. These frameworks aim to create safer workplaces through accountability, risk management, and participation.
Health And Safety At Work Act 2015
The Health and Safety at Work Act 2015 (HSWA) is New Zealand’s core workplace safety law. It applies to nearly all work environments, focusing on preventing harm to health, safety, and welfare. Employers must take all reasonable steps to identify and reduce risks. This involves assessing things like physical and mental behaviours that could lead to harm, such as fatigue or substance impairment. HSWA highlights the importance of leadership and collaboration, requiring businesses and workers to share responsibility for maintaining safety.
Supporting Regulations And Guidelines
HSWA is complemented by specific regulations and guidelines that address workplace hazards in more detail. These include rules for handling hazardous substances, operating machinery, and managing workplace ergonomics. WorkSafe NZ publishes these resources to provide industry-specific advice, ensuring businesses understand their obligations. For example, proper labelling, emergency planning, and worker training are critical for compliance. Adhering to these detailed standards helps businesses meet legal requirements and foster a proactive safety culture.
Primary Roles And Responsibilities
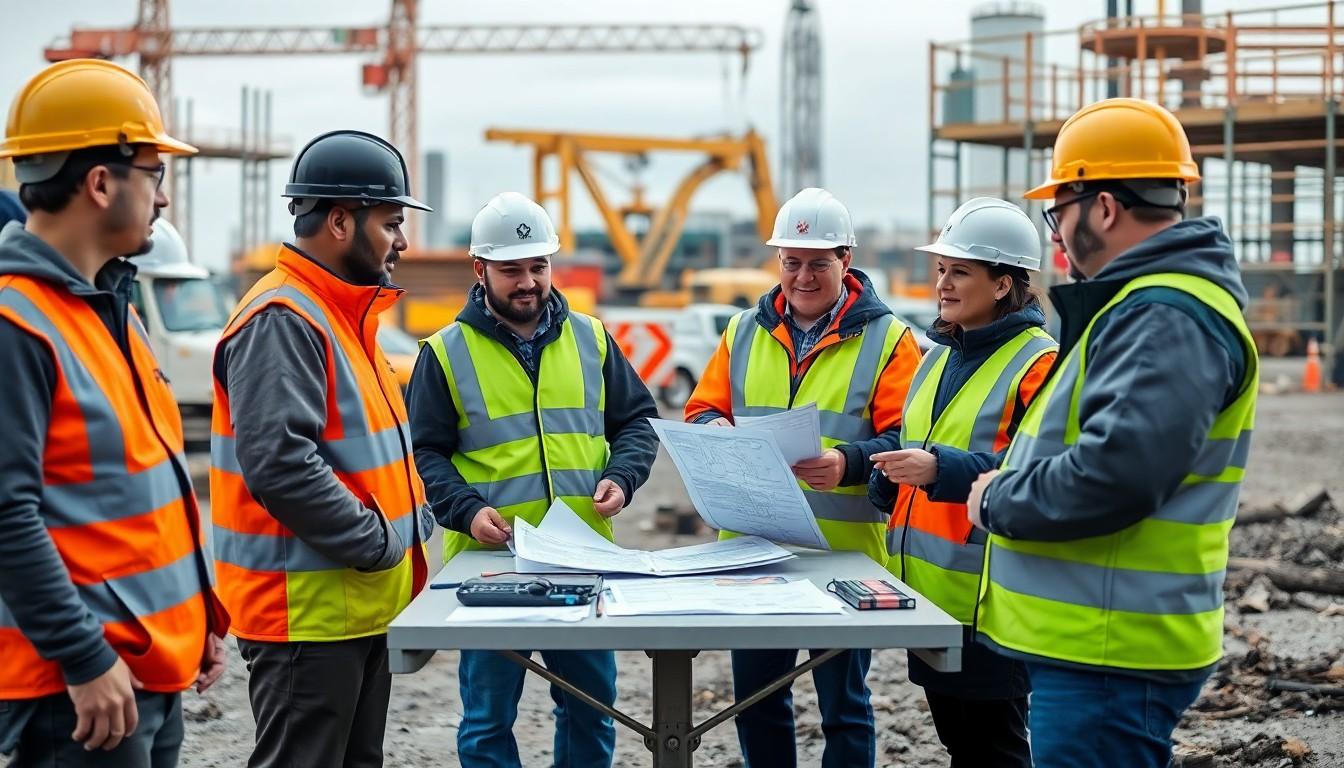
WorkSafe NZ’s regulations define clear duties for everyone involved in a workplace. Whether you’re a PCBU, a worker, or someone visiting a site, there are specific responsibilities to keep workplaces safe and compliant.
Duties Of PCBUs
Persons Conducting a Business or Undertaking (PCBUs) hold primary responsibility for workplace health and safety. You’re required to identify and minimise risks as much as reasonably practicable. This includes consulting with workers on safety matters and involving them in decisions about risks or hazards they might face.
If you design, manufacture, import, supply, install, or commission plant, substances, or structures, your duties as an “upstream PCBU” extend to ensuring these materials are safe for workplace use. For example, when commissioning a machine, it must undergo proper adjustments and inspections to confirm it meets safety requirements before use. PCBUs must also collaborate with others when duties overlap, ensuring effective coordination of health and safety measures.
Worker Engagement And Participation
Workers must have meaningful opportunities to contribute to improving workplace safety. As a PCBU, you’re expected to engage with your workers, listen to their concerns, and act on them to address risks. Worker participation can happen directly or through representation like Health and Safety Representatives (HSRs) or Committees (HSCs).
Your practices should empower workers to report hazards, identify unsafe practices, and share ideas for safer operations. Encourage open communication so workers feel valued in shaping their workplace’s health and safety standards.
Duties Of Other Workplace Participants
Everyone at a workplace has responsibilities, not just PCBUs and workers. Visitors, volunteers, and others are expected to take reasonable care for their own safety and avoid actions that might harm others. For instance, if you’re visiting, following safety instructions and staying aware of hazards is crucial.
Workers themselves have a duty to take reasonable care to keep themselves and others safe while working. This includes following safety practices and reporting hazards or unsafe conditions immediately. These shared responsibilities create a safer environment for everyone involved.
Managing Workplace Risks And Hazards
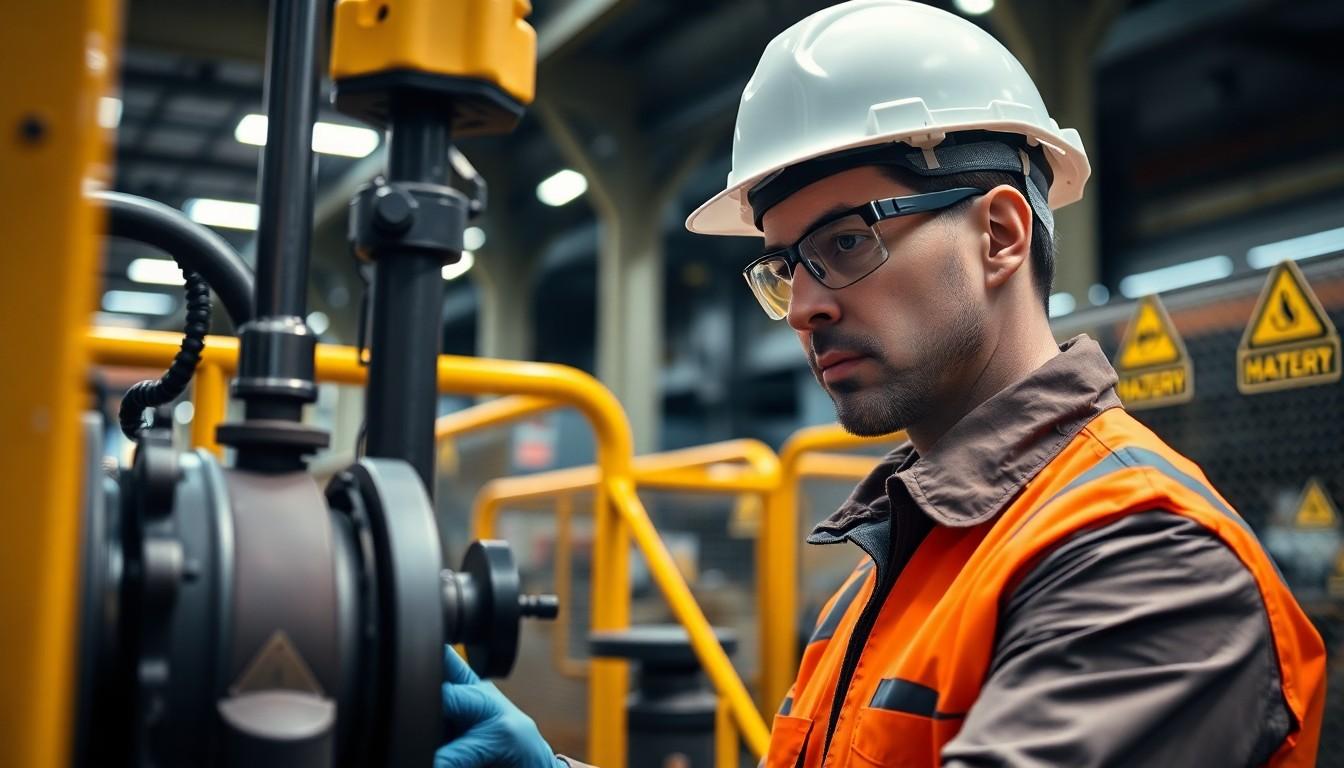
Effectively managing workplace risks and hazards helps create a safer work environment. WorkSafe NZ regulations outline clear steps to minimise potential dangers.
Identifying And Controlling Hazards
Identifying workplace hazards involves spotting anything that could potentially cause harm. The Health and Safety at Work Act 2015 (HSWA) requires employers, or PCBUs, to assess and manage risks that are reasonably foreseeable. These include physical hazards like uneven flooring and faulty machinery and chemical hazards like toxic substances.
Once hazards are identified, control them by following the hierarchy of controls. Eliminate hazards where possible, such as removing dangerous equipment. If elimination isn’t practical, minimise risks by substituting with safer options, isolating dangers, or using engineering controls like safety barriers. Administrative actions, like safety protocols, and personal protective equipment (PPE) are last resorts when addressing risks. Review these measures regularly to ensure they’re still effective.
The Role Of PPE And Health Monitoring
PPE acts as the final defence against unavoidable risks. Items like hard hats, gloves, and safety goggles reduce potential harm when hazards can’t be fully eliminated. Ensure workers know how to properly use and maintain PPE to maximise its effectiveness.
Health monitoring goes further by checking workers for signs of potential harm. Regular tests like spirometry for lung function or audiometry for hearing loss help measure the effectiveness of workplace controls. If health monitoring highlights exposure to risks, it’s essential to revise the control measures in place to better protect workers.
Emergency Preparedness And First Aid
Emergency preparedness ensures your workplace is ready to handle unexpected situations. WorkSafe NZ regulations require having clear emergency response plans tailored to potential risks in your workplace. These should include procedures for evacuations, chemical spills, and fires, and all workers should receive regular training to follow them effectively.
First aid is equally critical. Stock an accessible kit and ensure trained first aiders are available on-site at all times. Familiarity with these processes can significantly reduce harm in emergencies, preventing minor incidents from becoming major health and safety issues.
Regulatory Compliance And Enforcement
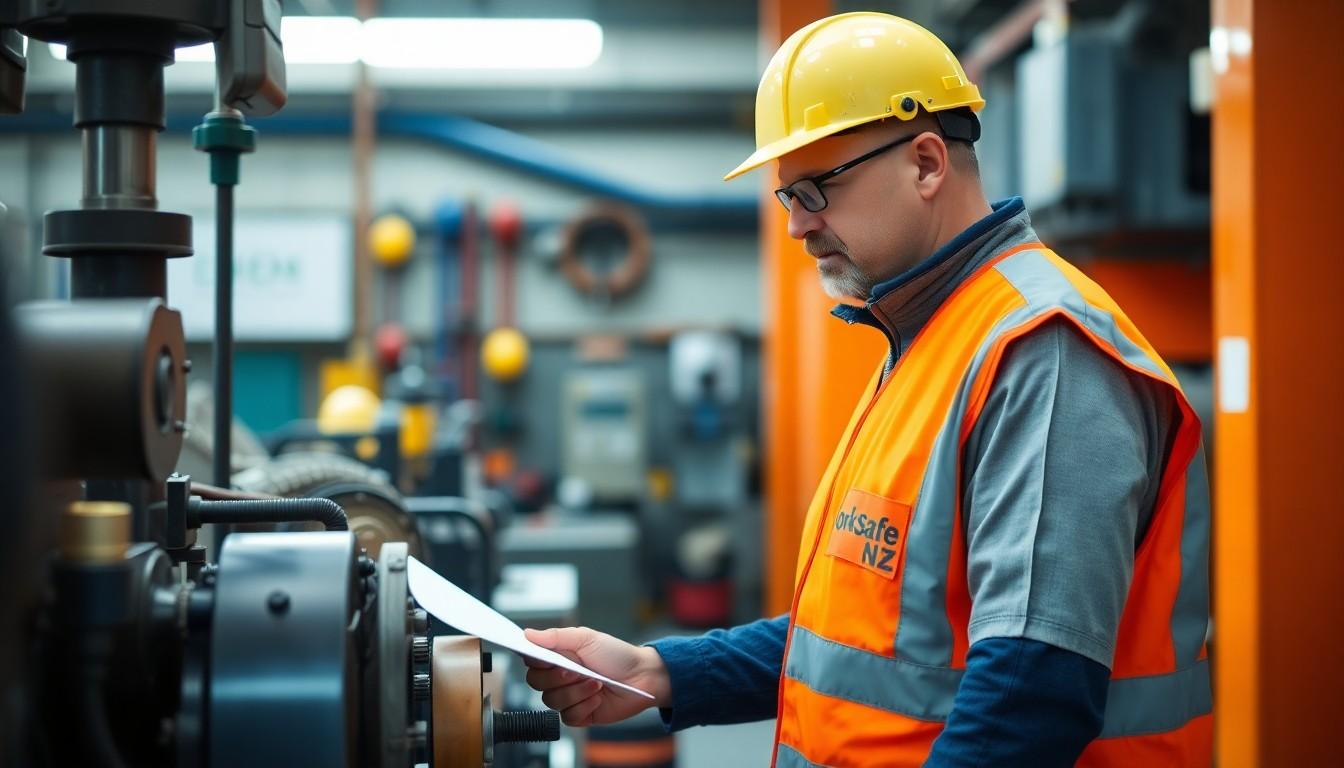
Understanding how WorkSafe NZ ensures compliance helps you maintain a safe and legally compliant workplace. Their enforcement approach balances education with regulatory action.
Notifiable Incidents And Reporting
A notifiable incident is any unplanned workplace event exposing someone to serious health or safety risks, such as fires, collapses, or electric shocks. Examples include gas leaks, equipment failures, or structural collapses. When these occur, you’re required to inform WorkSafe promptly. The site must remain undisturbed until authorised by an Inspector, except to assist injured persons or prevent further harm. This obligation ensures proper investigation and accountability.
Notifiable events also include deaths and specific illnesses or injuries tied to workplace operations. Detailed steps on what to report and how are outlined in WorkSafe’s guidance materials. Accurate and timely reporting lets regulators assess risks effectively and respond as needed.
Inspections And Enforcement Actions
WorkSafe Inspectors carry out inspections to check compliance, investigate incidents, and address risks. These visits might follow workplace emergencies, deaths, or serious injuries. Inspectors have authority to enter workplaces, take photographs, perform tests, and ask for compliance-related documents. If breaches of health and safety laws are found, Inspectors decide on appropriate actions.
Enforcement measures range from issuing improvement or prohibition notices to criminal prosecutions. Depending on the situation, Inspectors might also provide directive advice through formal letters or verbal warnings. These actions address immediate risks while encouraging businesses to maintain ongoing compliance.
Supporting Safe Work Practices
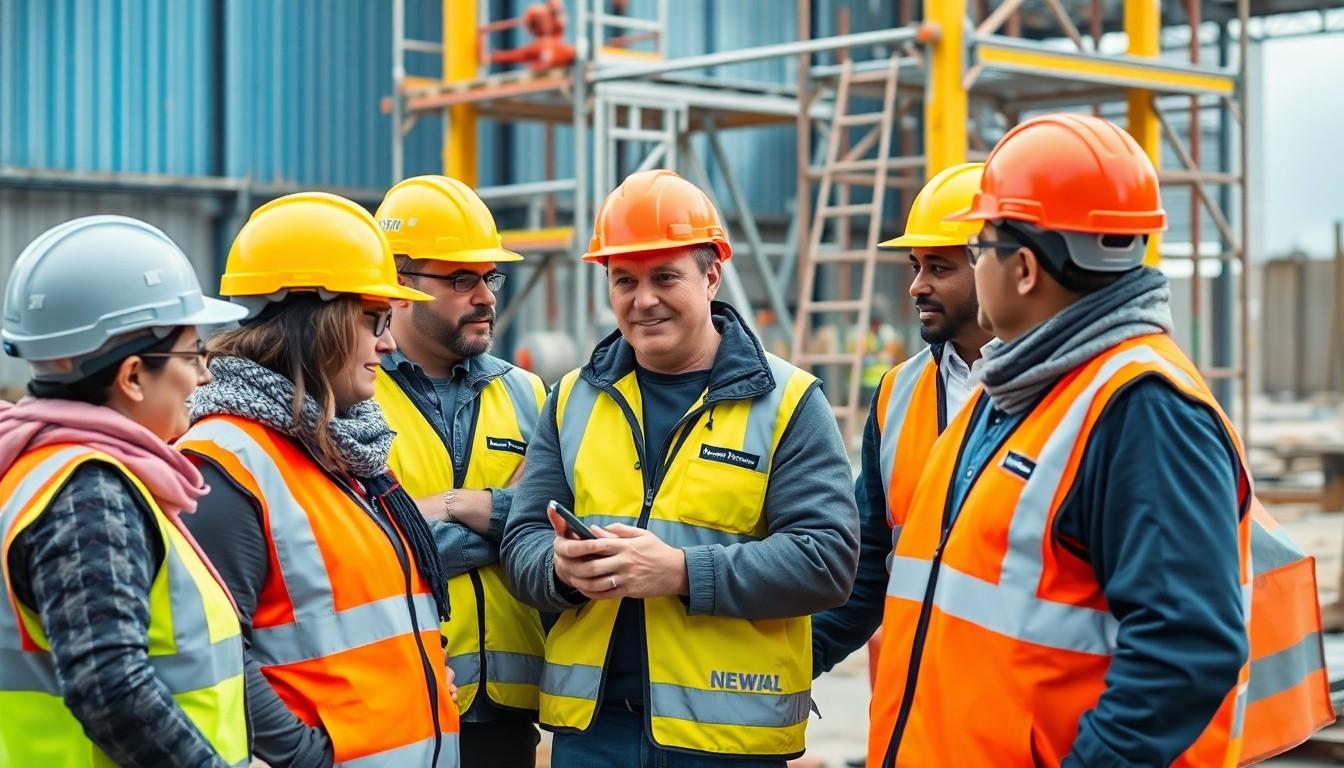
Creating a secure workplace goes beyond compliance. It’s about using practical tools, resources, and support to foster a safety-first culture.
Safe Work Instruments And Codes Of Practice
Safe Work Instruments (SWIs) are technical rules tied to regulations that clarify how to meet legal requirements. For instance, they cover variations in control measures for specific substances, ensuring these are handled safely. SWIs simplify complex regulations, making it easier for you to carry out them.
Codes of Practice, on the other hand, offer detailed guidelines for various risks, like safe scaffolding or managing hazardous chemicals. While not legally binding, they’re recognised standards, so following them shows that you’re taking reasonable steps to ensure safety. These resources help you align your practices with WorkSafe NZ standards.
WorkSafe NZ Guidance And Resources
WorkSafe NZ provides practical tools and information to simplify safety management. You can access free templates for hazard registers and safety policies, saving time on drafting paperwork. Training workshops build your knowledge about risk assessment, incident reporting, and emergency handling.
Incident reporting systems available through WorkSafe help you document workplace incidents accurately, ensuring transparency. Engaging with these resources lets you manage risks effectively while meeting compliance standards.
Conclusion
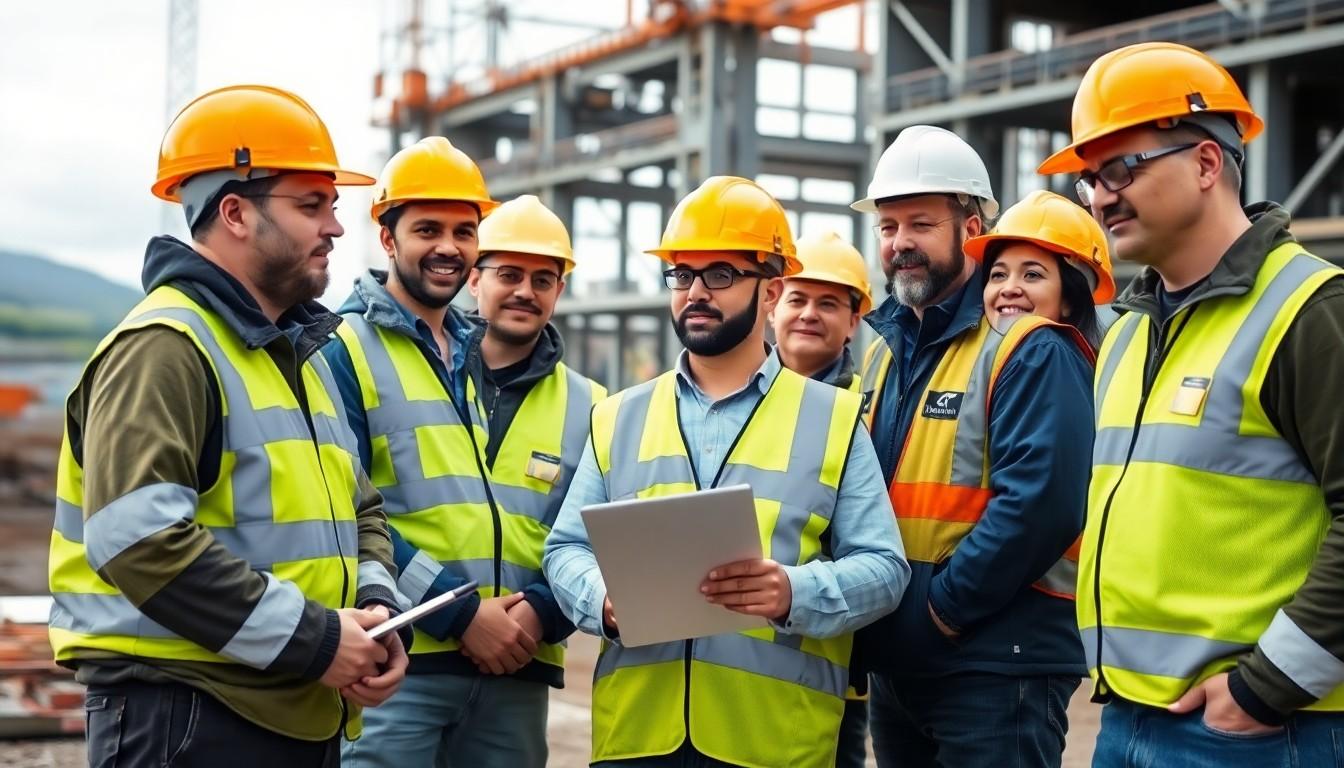
Understanding WorkSafe NZ regulations brings clarity to workplace safety expectations. These rules aim to reduce risks, protect health, and create safer environments for everyone involved. By actively engaging workers, implementing proper controls, and maintaining emergency preparedness, you’re contributing to a culture prioritising safety.
WorkSafe NZ provides resources to help businesses meet their obligations. Guidance, tools, and training from WorkSafe ensure legal standards are clear and achievable. Using Safe Work Instruments and adhering to Codes of Practice further demonstrates a dedication to safety, even beyond compliance.
Managing risks effectively and reporting incidents promptly strengthens accountability in your workplace. With a focus on practical measures and collaboration, you foster a proactive safety-first mindset.
Frequently Asked Questions
What is WorkSafe NZ, and what does it do?
WorkSafe NZ is New Zealand’s primary workplace health and safety regulator. It aims to promote and enforce safety standards in workplaces by providing guidance, resources, and training to reduce risks, prevent injuries, and ensure compliance with health and safety laws.
What is the Health and Safety at Work Act 2015 (HSWA)?
The HSWA is New Zealand’s core workplace safety legislation. It requires businesses to identify and manage risks to workers’ health and safety, fostering a shared responsibility between employers and employees to maintain a safe work environment.
What are the responsibilities of PCBUs in workplace safety?
Persons Conducting a Business or Undertaking (PCBUs) are responsible for ensuring workplace safety by identifying risks, consulting workers on safety matters, providing safe tools and materials, and maintaining a safe environment for all participants, including visitors and volunteers.
How does WorkSafe NZ support businesses in meeting safety obligations?
WorkSafe NZ offers industry-specific resources, training workshops, templates for hazard management and safety policies, and Safe Work Instruments (SWIs) that clarify compliance requirements. These tools help businesses understand and meet their legal responsibilities.
Why is worker participation important in workplace safety?
Worker participation ensures that employees have a voice in identifying hazards, suggesting improvements, and contributing to safety decisions. Establishing health and safety committees or appointing representatives encourages collaboration and creates a safer workplace.
What are the regulations for handling hazardous substances?
WorkSafe NZ enforces strict rules for handling hazardous substances, including proper labelling, secure storage, and emergency plans. These measures aim to minimise risks and prevent workplace accidents involving dangerous materials.
What should businesses do to prepare for emergencies?
Businesses must develop tailored emergency response plans, train employees on procedures, and ensure access to first aid. This preparedness reduces harm during unexpected events and ensures quick, effective responses to workplace emergencies.
What are notifiable incidents, and when should they be reported?
Notifiable incidents are unplanned events that pose serious health or safety risks, including injuries, fatalities, or exposure to hazardous substances. These must be reported to WorkSafe NZ immediately to allow prompt investigation and compliance reviews.
What is the hierarchy of controls for managing workplace risks?
The hierarchy of controls prioritises effective risk management measures: eliminate the hazard, substitute it with a safer alternative, implement engineering controls, use administrative processes, and rely on personal protective equipment (PPE) as a last resort.
What happens during a WorkSafe compliance inspection?
WorkSafe inspectors assess whether businesses are meeting health and safety laws by inspecting workplaces, conducting risk assessments, and reviewing procedures. They may issue improvement or prohibition notices and take further action for non-compliance if necessary.